H13 (4Cr5MoSiV1) is a hot-working die steel widely used in the world. It has high thermal strength and hardness
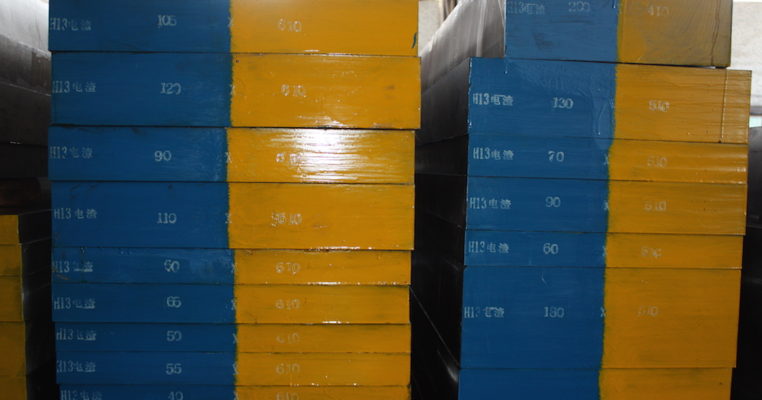
H13 (4Cr5MoSiV1) is a hot-working die steel widely used in the world.
It seems I had wrote much about H13 die steel but my friends told me that it’s ramdon data,they want a complete data,so I serch alot,and organized it.
It has high thermal strength and hardness, high wear resistance and toughness, and good thermal fatigue resistance. Hot extrusion dies and die casting dies for aluminum, copper and their alloys. Hot work die steel is subject to large impact loads, strong friction, thermal stress caused by severe cold and heat cycles, and high temperature oxidation, and often failure modes such as chipping, collapse, wear, and cracking.
AISI H13 Chemical composition
C(%) | 0.32~0.45 | Si(%) | 0.80~1.20 | Mn(%) | 0.20~0.50 |
P(%) | ≤0.030 | S(%) | ≤0.030 | Cr(%) | 4.75~5.50 |
Mo(%) | 1.10~1.75 | V(%) | 0.80~1.20 |
Its chemical composition characteristics:
① Medium carbon, with a mass fraction of 0.32 to 0.45%, to ensure high hardness, high toughness and high thermal fatigue resistance.
② Add more elements Cr, Mn, Si to improve hardenability. Mn can change the nature and shape of the oxides formed during solidification of the steel, avoid sulfur forming low melting point FeS on the grain boundaries, and exist as a certain plastic MnS, thereby eliminating the harmful effects of sulfur and improving the heat of H13 die steel Workability; Cr and Si can improve tempering stability.
③ Add elements Mo and V that cause secondary hardening. Mo and V can also prevent the second type of tempering brittleness and improve the tempering stability.
The failure problem of H13 steel mold is a very complicated technical problem, which can be analyzed from four aspects: material, design, manufacturing and use.
Chemical composition and metallurgical quality
H13 die steel is a type of hypereutectoid alloy steel. There are many defects in the structure such as non-metallic inclusions, carbide segregation, center porosity and white spots, which greatly reduce the strength, toughness and thermal fatigue resistance of mold steel. H13 steel is generally divided into ordinary H13 steel and high-quality H13 die steel according to quality. Due to the use of more advanced production technology, high-quality H13 steel has pure steel, uniform structure, slight segregation, and higher toughness and thermal fatigue properties. Ordinary H13 steel must be changed to forge to crush large non-metallic inclusions, eliminate carbide segregation, refine carbides, and homogenize the structure.
Mould Design
When designing the mold, the external dimensions of the module should be determined according to the material and geometric dimensions of the formed part to ensure the strength of the mold. In addition, excessively small fillet radii, wide and thin wall sections with wide and thin wall sections, and improper positions of holes and grooves can easily cause excessive stress concentration and initiation of cracks during mold heat treatment and use. Therefore, avoid sharp corners as much as possible in the design of the mold, and the holes and slots should be arranged reasonably.
Ms Sharon Wan
Mobile/WhatsApp: 0086-13580960968
Tel: 0086-769-23190193
Fax: 0086-769-88705839
Email: Sharon@otaisteel.com