H13 application –Chapter 9
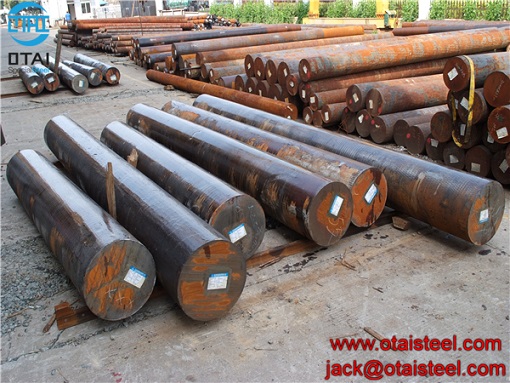
The design of mold depends on the shapes and specifications of products to make sure the size of the die for H13. H13 die steel was good for the strength of die in tooling steel.
Furthermore, too small a radius of a rounded corner, ill-suited groove position and etc will make the die gets big pressure during the heat treatment. H13 is easy to cause crackle. So H13 must make the taper angle, hole and etc at the right position in the mold.
- Production technique-H13
- Forging ProcessThere are so many alloy elements in H13 steel. The resistance of deformation is big at the time of forging. And the thermal conductivity of the material is bad. So the eutectic temperature is low. H13 is easy to burn. So the preheated temperature range must be at 800-900℃. Then heated to the initial forging temperature of 1065-1175℃. In order to crush large non-metallic inclusions and make the carbide get small, the forging ratio needs to be bigger than four. At the cooling process after forging, it is possible to get quenching crack. And the core is easy to get transverse cracks. So H13 steel must be slowly cooled after the forging. The machining of cutting The roughness of the surface of H13 after the machining of cutting, H13has a large impact on the thermal fatigue property of steel mold. The roughness of the steel mold surface of H13 must be lower. The knife mark and cullet cut are not supposed at here. Those shortages will cause pressure over control to make the thermal fatigue crack. So, must pay attention to handle these things in the mold at the time of processing. 3. The machining of grinding At the process of grinding, the generation of heat by friction at the parts which is easy to cause the problems of crack, pyrosis and etc.