Imagine that if you stop after forging Cr12MoV steel, allow the austenite to recover and start to recrystallize, and then quench immediately, it can inhibit the growth of austenite grains, and also inhibit the re-aggregation and hornification of carbides.
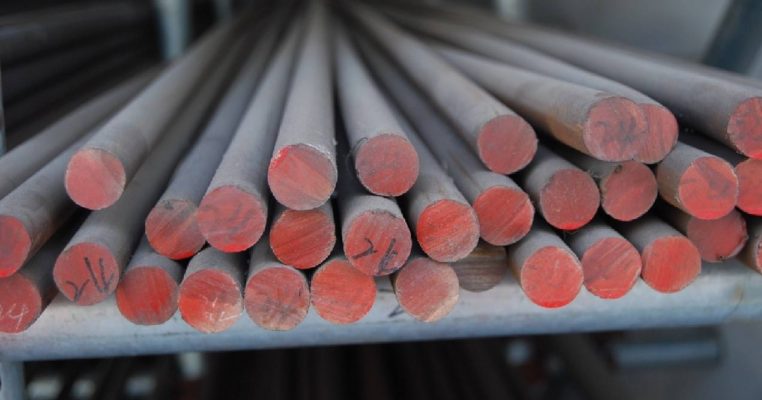
Waste heat quenching-double refinement Forging Cr12MoV steel process
(1)
During the forging Cr12MoV steel process, there are two contradictory factors at play: on the one hand, the hammering effect of forging, which causes the carbide to be broken and broken, and the austenite is seriously deformed; on the other hand, the Forging Cr12MoV steel temperature,it is higher and the deformation,The subsequent austenite immediately recovered,and recrystallized in the gap between hammers, and then began to grow. The crushed carbides also re-gathered with the hammer gap and gradually horned. The effect of temperature is continuous, and the refinement of hammering is intermittent. If the forging ratio is not enough, the stopping forging temperature is too high, and the number of fires is too large, the grains will be coarsened, the carbides will be coarse and multi-angled, the fracture of the workpiece will be coarse-grained, and the corners will be brittle.
(2)
When the sintering is stopped and slowly cooled, the carbides will grow, the carbon in the austenite is precipitated continuously, and the carbides are gradually keratinized, or the carbide keratinization is mostly formed during the sintering and slow cooling. The higher the forging temperature, the slower the cooling rate after forging, and the more severe the coarsening and horning of austenite grains and carbides. The sharp corners of carbides ,they are the focus of stress concentration and the source of fracture,which for early brittle failure of tool and die. Changing the distribution and morphology of carbides,it can extend the service life of the tool and die.
(3)
Imagine that if you stop after forging Cr12MoV steel, allow the austenite to recover and start to recrystallize, and then quench immediately, it can inhibit the growth of austenite grains, and also inhibit the re-aggregation and hornification of carbides. A relatively satisfactory carbide particle size and morphology can be obtained, which is the theoretical basis of the forging waste heat quenching process. If combined with appropriate firing times and forging ratios, we can explore the best forging waste heat quenching process scheme to obtain the effect of double refinement of carbides and austenite grains.
Ms Sharon Wan
Mobile/WhatsApp: 0086-13580960968
Tel: 0086-769-23190193
Fax: 0086-769-88705839
Email: Sharon@otaisteel.com