D2 tooling steel -Chapter 5
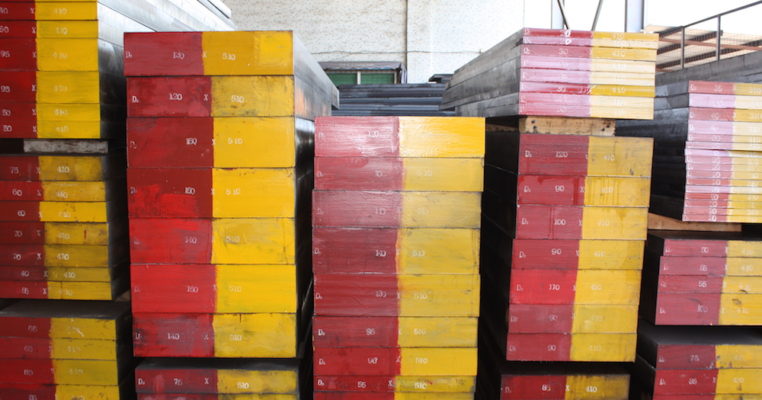
CHAPTER 5 OTHER FEATURES
Sometimes features added to a blade for user convenience, like friction grooves on the blade spine, can create stress risers that negate the resistance to blade breakage of zone-edge hardening. Sometimes different production lots of steel exhibit different reactions to zone hardening due to allowable fluctuations in chemical composition. User discretion is the single most predictable way to avoid blade failure from lateral flexing. D2 is probably not the best choice of steel to make sharpened pry bars from, even with zone-edge hardening.
The downside to the nano-grain of the friction-forged edge is it exhibits less “tooth” for reduced cutting efficiency while carving materials like plastic and seasoned wood. Since the first four knives produced by Diamond Blade were primarily hunting knives for processing harvested game, rather than bushcraft, this is probably not a significant issue to Diamond Blade knife users. The knives can cut more meat and hide between sharpening, as only the “best of the best” can.
BUSHCRAFT AND UTILITY KNIVES
For bushcraft and utility applications, I would choose a D2-bladed Knives of Alaska model from this sister company which is also run by Diamond Blade’s managing partner Charlie Allen. The KOA D2 blades are conventionally heat treated, double-draw tempered and cryo-treated for remarkable performance in their own right. They just don’t match the Diamond Blade for overall cutting endurance between sharpening.
Yet another way to produce knife blades out of D2 steel alloy is by casting the blade blank out of molten D2 steel. The blank is then finish-ground and heat treated to individual specifications. Selected handle materials help to create each cast blade into a distinctively individualized knife.
Cast D2 is sometimes called Dendritic D2. The proponents of this production method believe the steel grain of the blade has more predictable properties from casting, then what can be attained with other methods. They claims to have more consistent carbide structure at the blade edge and longer cutting endurance. Of course edging, alloy content and final heat treatment still play a dominant role in determining the performance of each finished knife, regardless of steel production or blade-creation methodologies.
D2 is not an alloy used for forged knives with any frequency. The steel is difficult to move with a hammer and prone to decarburizing when it’s heated high enough for easier metal movement. D2 is occasionally incorporated into Damascus blades, but there have been problems with some D2 Damascus experiencing de-lamination of the layers under lateral stress.