1.2738 plastic mold steel is the German DIN standard material number.
The hardness levels of 1.2311 and 1.2738 plastic mold steel are generally 28-34HRC. 1.2311 is mainly used for small size molds, the thickness is generally up to 400mm. For larger sizes, 1.2738 alloys with Ni added are usually used. When the hardness of 1.2711 is about 42HRC, better polishing performance can be obtained.
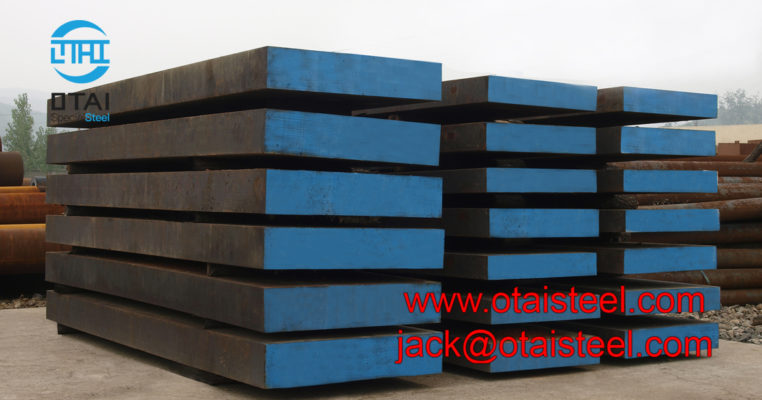
1.2738 plastic mold steel is improved on the basis of P20 steel, and 0.9% ~ 1.2% Ni is added on the basis of P20 steel. So its toughness, plasticity and corrosion resistance can be significantly improved. It is a widely used steel for plastic molds in the world. It has good comprehensive mechanical properties and high hardenability. It can make the steel with a larger cross-section more uniform in hardness. It has good polishing performance and a high surface finish.
When the steel is used to make a mold, it is generally tempered first, and the hardness is 28-35HRC (that is, pre-hardened), and then it is made into a mold by cold working and can be used directly. In this way, the performance of the mold is guaranteed, and the deformation of the mold caused by heat treatment is avoided. Therefore, the steel is suitable for manufacturing large and medium-sized plastic molds.
Since P exists in the solid solution of ferrite, it tends to segregate at the grain boundaries. It reduces the toughness of the steel. Therefore, the P content in the steel should be as low as possible.
1.2738 plastic mold steel is mainly used in large plastic molds such as car front bumpers and home appliances. So it has high requirements on isotropy and polishing performance. While S tends to segregate at the grain boundary, increasing the anisotropy of steel, and the resulting Sulfide inclusions reduce the purity of the steel. So the S content in the steel should be as low as possible.
Due to the differences in technical strength and production equipment of various steel mills, the quality level of various types of 1.2738 plastic mold steel on the market varies. So it really is very important and necessary to find a supplier with very good reputation. And we with over 21 years’ pre and after sales business on the special steel, we could help distributor and end users to avoid all possible cheat.
Tel: 0086-769-23190193
Fax: 0086-769-88705839
Email: jack@otaisteel.com