The manufacture of H13 hot work die steel molds has to go through a series of process links such as design
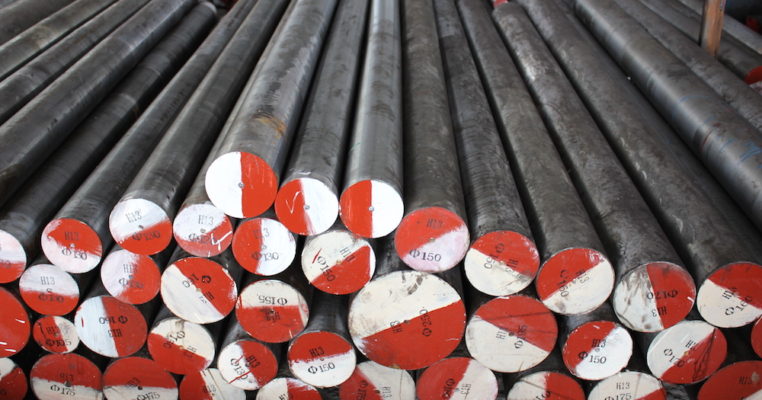
The manufacture of H13 hot work die steel molds has to go through a series of process links such as design, material selection, forging, annealing, machining and heat treatment. Improper process design or process operation in each process link will cause premature failure of the mold and reduce the service life of the mold. Hot work die steel often appears in the form of failure such as chipping, collapse, wear and cracking. The form, degree and location of failure of hot work die steel record the design, material selection, forging, annealing, machining and heat treatment to a series of process links. Important information.
Observe and analyze the macroscopic morphology, microstructure and failure form of the H13 hot work die steel mold at the failure location, and use theories and methods of metallography, material physics, and fracture mechanics to suggest the macromorphological features and materials at the H13 steel mold failure location The relationship between microstructure and failure form and mold design, material selection and processing technology, so as to propose scientific and reasonable process improvement measures.
(1) Analysis of chemical composition and metallurgical quality of raw materials
Improving the cleanliness of H13 hot work die steel, especially reducing the sulfur content is an effective measure to improve the life of H13 steel molds. The sulfur content of high-quality H13 steel is between 0.005 and 0.008%. H13 steel is a hypereutectoid steel with a relatively high alloy element content. Carbide segregation occurs during smelting and casting. The ingots form coarse carbide segregation zones after forging and rolling. Carbide segregation zone and casting residual dendrites, shrinkage, porosity and inclusion directly affect the microstructure and properties of H13 steel mold, which is one of the important reasons for the early failure of the mold. The analysis of the chemical composition and metallurgical quality of the raw materials can assess whether the raw materials are qualified, which can be used to guide the formulation of scientific and reasonable forging processes and heat treatment processes.
Test method
Sampling raw materials of H13 hot work die steel, analyzing its chemical composition, and assessing whether the chemical composition meets the requirements; cutting the sample from the center of the steel, grinding and polishing, etching with 4% nitric acid alcohol solution, inspecting it on an optical microscope Microstructure, grade of carbide segregation zone and inclusion grade according to relevant national technical standards.
(2) Analysis of mold microstructure
Microstructure analysis can determine whether there is carbide segregation zone in the mold failure location, large non-metallic inclusions, network carbides, eutectic carbides and tempered martensite; micro-area composition analysis can determine the chemical composition of the mold failure location Distribution characteristics; microhardness analysis can determine the mechanical properties of the mold failure location. Comprehensively analyze the microstructure, micro-hardness and micro-area composition at the failure location of the mold, reveal the macroscopic morphological features and the micro-mechanism of the failure form at the failure location of the mold, and correctly evaluate the current forging, spheroidizing annealing, quenching and tempering Technology, so as to propose scientific and reasonable process improvement measures.
Test method: Cut the sample from the failure position of the mold, grind and polish it, etch it with 4% nitric acid alcohol solution, inspect the microstructure on an optical microscope or scanning electron microscope, measure the hardness on a microhardness tester, Microdomain composition was determined on a spectrum analyzer.
Ms Sharon Wan
Mobile/WhatsApp: 0086-13580960968
Tel: 0086-769-23190193
Fax: 0086-769-88705839
Email: Sharon@otaisteel.com