High Speed Steel –M2 Part 2
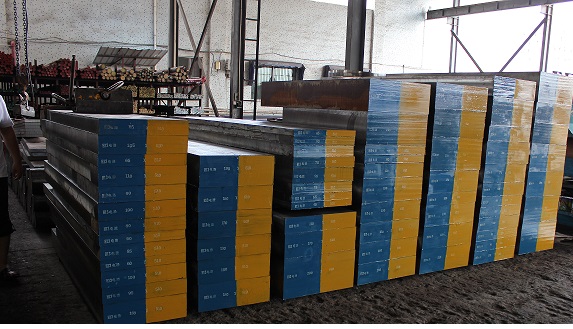
M2 high-speed steel is a tungsten-molybdenum tool steel. M2 is characterised by well-balanced toughness, wear resistance and red hardness properties.
AISI M2 high-speed steel has largely replaced T1 in most applications due to its superior properties and advantageous pricing. M2 is medium-alloyed and is a good all-round performer with good machinability, in this respect it is superior to the high alloyed cold work steels.
Related Specifications : DIN 1.3343
Applications
The well balance properties of M2 means it is used in a wide range of cutting tools where demands for hot hardness are moderate, such as twist drills, reamers, broaching tools, milling tools, taps and metal saws.
M2 is also suitable for cold work applications such as tools for punching, forming and pressing.
If you are looking for superior red-hardness then consider M42 high speed steel.
M2 high-speed steel stock
Steel Express stock and supply M2 high-speed steel in round, flat and square bar. We can cut to your requirements in house.
M2 diameters from 10 mm up to 250 mm. Flat and square stock, please call with your requirements .
Heat treatment of M2 high-speed steel
The following information is provided for guidance only. The rate of heating, cooling and soaking times will vary due to the shape and size of each component and other external factors.
Annealing
Heat the M2 high-speed steel to 850 – 900°C. Hold at temperature for at least two hours or one hour per 25 mm of thickness. Furnace cool slowly. The maximum hardness should be 248 Brinell.
Stress relieving
Stress relieving M2 is recommended after machining or grinding and before hardening to minimise the chance of distortion. Heat the component to 600 – 700°C and soak well (for approximately two hours), then cool in air.
Hardening
Pre heat the M2 in two steps; 450 – 500°C then 850 – 900°C. Then continue heating to the final hardening temperature of 1200 – 1250°C. Do not leave the steel too long at the hardening temperature. Quench in warm oil or brine to about 500°C then air cool down to room temperature.
Tempering
Heat the M2 to the required tempering temperature, hold at temperature for at least two hours or one hour per 25 mm of thickness. Double tempering is recommended.
Forging
Pre heat slowly to 850 – 900°C, then increase more quickly to the forging temperature of 1050 – 1150°C. Do not forge below 880 – 900°C. Cool very slowly after forging.
(data sheet & typical analysis available on request).
Properties
M-2 is typically bought to meet chemistry requirements rather than physical requirements. For that reason, physical properties are generally not provided unless requested prior to production. Any material can be sent to a third party after production to be tested for physical properties.
Typical Uses
Typical Applications include Broaches, Boring Tools, Chasers, Cold Forming Rolls, Cold Heading Inserts, Drills, End Mills, Form Tools, Hobs, Lathe and Planer Tools, Punches, Milling Cutters, Taps, Reamers, and Saws.