H13 STEEL APPLICATION IN LIFE-Chapter 9
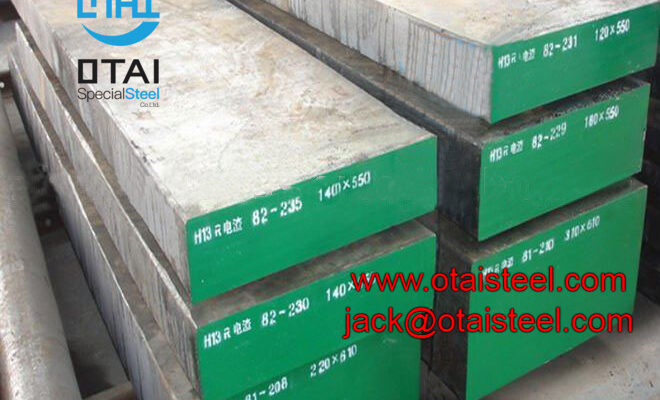
Like all dies, however, H13 steel is regrettable that they are not really permanent. An aluminum casting weighing up to 1 kg might be produced tolerably well for up to 80 000 or 100 000 shots before the die will require to be refurbished as a result of heat checking (cracks due to thermal fatigue of the die surface that produce a network of unsightly raised fins on the cast surface of H13 Steel).
Magnesium alloy high-pressure die castings of H13 steel are much kinder to dies, giving perhaps five times or more life. This is partly the result for H13 steel the lower heat content of Mg alloys, and partly because of the low solubility of iron in liquid magnesium that reduces its action to dissolve the die surface. In contrast, liquid Al has a relatively high solubility of iron, resulting in a phenomenon known as ‘soldering’ of the casting to the die. This action is particularly destructive to dies. It is countered to some extent by the addition of high levels of iron to high-pressure die-casting alloys, thus pre-saturating the liquid metal with iron and so greatly reducing the tendency for the melt of H13 steel to dissolve the die.
Attempts have been made to cast of H13 steel molten stainless steels by high-pressure die casting. In this case of H13 steel the only die material of H13 steel capable of withstanding the rigors of this process was an alloy of molybdenum. Even these ‘moly’ dies suffered early degradation by thermal fatigue cracking, threatening the commercial viability of the process. So far as the author is aware, partially solid (inaccurately called ‘semi-solid’) stainless steels have not been extensively trialed. These cooler mixtures that have already given up practically half of their latent and specific heat during freezing would greatly benefit die life. The commercial viability of the somewhat more expensive mixture would remain a potential show-stopper of course for H13 steel .
Because of the very high pressures for H13 steel involved in HPDC internal cavities are usually limited to those formable by straight withdrawable steel cores. If the core cannot be withdrawn then the usual alternatives such as sand cores are totally unsuitable because they are penetrated by the liquid metal. One of the H13 steel is very few options to make undrawable cavities in HPDCs are salt cores described below.